with John Stephens, General Manager – Logistics, Grundon Waste Management
A Journey to Carbon Neutrality
Introduction
Grundon Waste management is the UK’s largest family-owned supplier of integrated waste management and environmental services. Its operating area stretches from its core Thames Valley base as far as Bristol in the south-west and Stansted in the east. As well as collecting commercial waste, it owns and operates industry-leading treatment facilities, including Energy from Waste (EfW) plants generating electricity for the National Grid. With customers ranging from major property management firms to leisure and hospitality facilities; universities, airports, and NHS Trusts; it has a reputation for innovation and investment in new technologies. It recently announced an ongoing annual £5 million commitment to investing in a greener, cleaner fleet; part of the company’s commitment to achieving net zero. To explain further, Essential Fleet Manager Magazine was delighted to catch up with John Stephens, General Manager, Logistics at Grundon.
Interview
Q: Could you give a brief history of the business, how it started and early innovations.
The Grundon story began in 1929 when Stephen Grundon (grandfather of our current chairman Neil Grundon) and his brother Les bought their first internal combustion vehicle – a 1915 Pierce-Arrow R8 3 Ton truck, which set the business on its path for the extraction and supply of aggregates. Grundon Sand & Gravel (as it became known) is still in business today and operates as a separate company.
The company expanded into associated areas, including excavation, demolition, haulage and bulk earth moving – bringing the first JCB into London to dig the foundations for what is now Brunel University.
By the late 1960s/early1970s, the environmental movement was beginning to find its feet and the Grundon family made the decision to focus more on waste management and the drive towards increasing recycling.
As the business began to take shape, so did the vehicle fleet, with the purchase of the first Grundon Rolonof – so named because the Scammel Routeman 8×4 30 tonne chassis vehicle had rollers that enabled a hook to roll the large metal container on and off the vehicle body.
In 1979, Grundon’s innovation credentials were underlined with the arrival of the UK’s first Front End Loader (FEL) vehicle. Imported from the US, it was a 30 cubic yard Garwood FL3000 FEL used to collect light packaging wastes from industry and commerce customers.
In the 1980s, the company introduced the now ubiquitous ‘wheelie bin’ to the UK; the following decades saw investment in facilities including a state-of-the-art Materials Recovery Facility (MRF) opened in 1996, and a joint venture Lakeside Energy from Waste (EfW), officially opened by the late Prince Philip, Duke of Edinburgh in 2010.
As the environmental agenda began to gather pace, Grundon began measuring its own carbon emissions in 2000 and, in 2014, became the first of the major waste industry players to adopt CarbonNeutral® certification across its vehicle fleet, offsetting its carbon emissions and ensuring that collections did not add to customers’ carbon footprint.
Now, nearly a decade later, comes the launch of Grundon’s repowered all-electric refuse collection vehicles – including one powered by customer waste – something we think is an industry first.
Q: Could you briefly introduce yourself and your background within fleet?
I joined Grundon Waste Management in 2011 as Depot Operations Manager for the company’s Beenham site, near Reading. Since then, the role has grown to include responsibility for waste collection operations, vehicle workshops, fabrication and Grundon’s operational training team.
Alongside that I support a number of large contracts, including Heathrow Airport, British Airways and numerous NHS Trusts; as well as overseeing Grundon’s waste management responsibilities at high profile British sporting occasions such as the Henley Regatta, Royal Ascot, Queens Club Tennis Championships, and events at Silverstone Circuit including the British Grand Prix.
I now have responsibility for around 500 staff, 11 operational depots and the company’s fleet of over 330 commercial vehicles, all of which keep me on my toes.
Q: What is the breakdown of your fleet assets in terms of numbers and vehicle types?
Our overall fleet totals 336 commercial vehicles, comprising:
(52) Rolonof – 32t
(29) Skip loaders – 18t
(24) Front End loaders – 32t
(144) Trade Waste – 12 – 32t
(36) Box/Curtainsider/double deck 7.5 – 44t
(23) APCr bulk tankers 44t
(20) Flatbed 12 – 26t
(8) Wet Vacuum tankers 18 – 44t
(from the above there are 71 trailers within the fleet)
(23) Small commercial vehicles (under 3.5t)
(124) Company cars, of which 68% are electric vehicles (EVs)
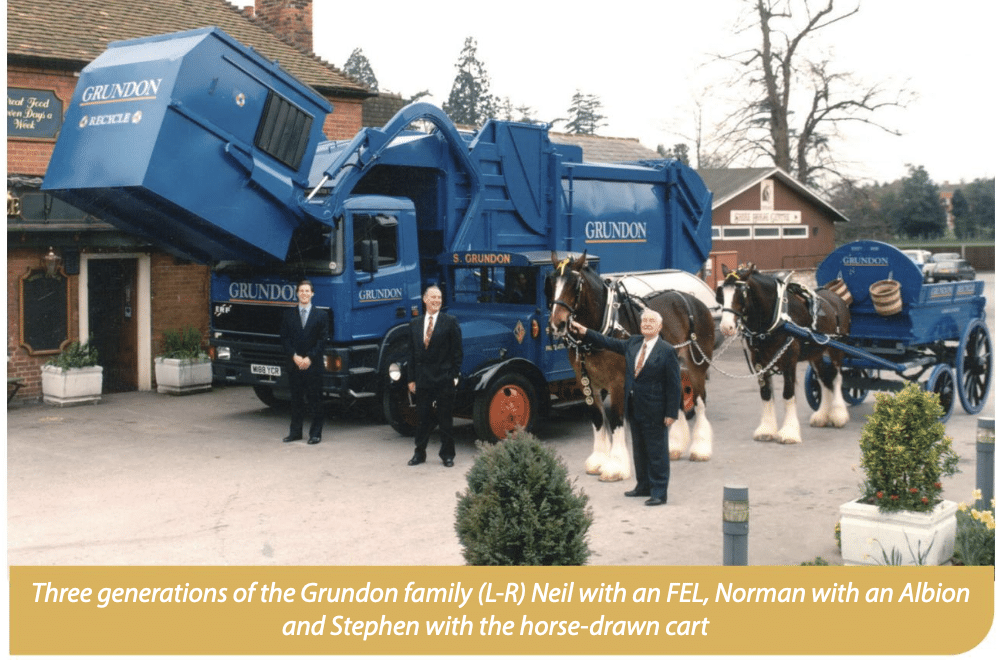
Q: During your journey towards lowering your fleet emissions and achieving net zero, what are the key challenges you have faced as a waste management service provider with such a complex and diverse fleet?
As far as our commercial waste collection fleet is concerned, the main challenge is that we can only be as good as the technology itself. By that, I mean when we are sending our new fully-electric waste collection vehicles out on their rounds, we have to be sure they have the battery capacity to complete them – and that is down to how quickly battery life technology develops.
When we started going down the EV road, we carried out very detailed trials in conjunction with our Gloucester-based partner Refuse Vehicle Solutions (RVS), a leader in the remanufacture of waste vehicles.
They lent us a trial electric vehicle as far back as autumn 2021, so we could run collection routes out of our Colnbrook depot in and around Central and West London, Slough and Windsor, testing the technology to understand the vehicle’s range and suitability.
We’re pleased to say it exceeded our expectations, completing average waste collections of around 120-140km per day and enabling us to press ahead with converting our existing diesel Mercedes-Benz Econic with a Dennis Eagle body waste collection vehicles to electric.
What sets us apart from fleet operators in other industries is our critical ‘must have’, because in addition to powering the vehicle, the battery technology also needs to be sufficient to drive all the necessary hydraulic and compulsion systems to manage collections, bin lifts and compaction processes.
It was described to us as effectively one big mathematical calculation and, thanks to RVS’s expertise we now have 280kW battery packs fitted to the vehicles, which provide the necessary capacity.
While the primary focus began with (and continues to be) conversions from diesel to electric, we also took the decision to purchase our first new Scania electric waste collection vehicle (due to arrive soon) to help speed up the overall electrification process. Further Scania EVs will be added to the fleet at a later date.
We are still very mindful of carefully choosing the EV routes and acknowledge that, at present, not all customer collection journeys may be suitable for our EV waste wheelers because of locations and charging opportunities. We work extremely closely with Scania, developing vehicles that are fit for our specific purposes, this closeness creates trust and harmonic drive to introduce alternative fuelled vehicles.
We are determined however, that as the technology progresses, more and more of our customers will be able to benefit from this clean technology and they, together with local communities and our own drivers, will see the increased benefits of our zero emission and zero noise collections.
The waste collection vehicles aside, we also operate a fleet of small commercial box vans up to 3.5 tonnes (typically used smaller volumes of hazardous and clinical wastes), these are next in line for change to EV along with our company cars. Sixty-eight percent of our company cars are already electric and, as the car fleet is gradually renewed, we expect it to be 100% electric within the next 18 months.
That’s obviously meant installing plenty of electric recharging points across all our locations, from offices to depots – 53 in total – quite a major undertaking and a significant investment; plus we have further plans to expand this area as more EVs are purchased.
Operating a tanker and articulated fleet with tractor units (largely used for clinical and hazardous wastes) also creates its own challenges when looking at alternative fuels.
Because these vehicles are much heavier and, in the case of our powder tankers especially, generally undertake much longer journeys, running them on electricity isn’t currently the best option.
We think hydrogen (or a hydrogen fuel cell) is likely to be the best alternative but at present, the technology and the refuelling options just aren’t there yet. In the meantime, we specify the cleanest, leanest Euro 6 diesel engines, and we also provide specific driver training to ensure they maximise fuel efficiency.
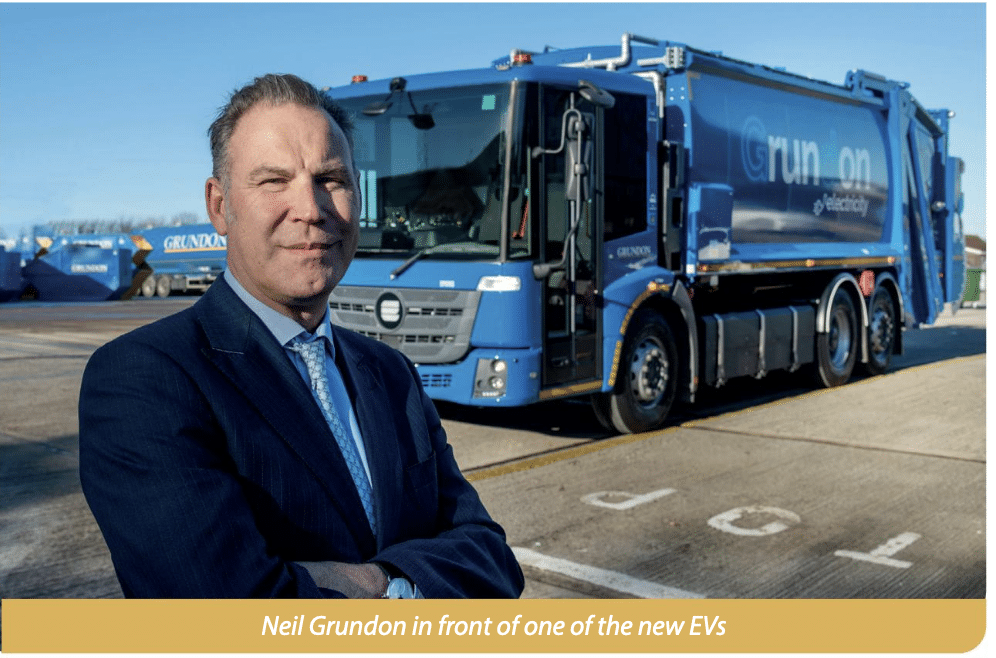
Q: In seeking replacements to your ICE powered vehicles, have you trialled or are you intending to trial any further alternatives to those already adopted within your fleet?
We take the view that we don’t want to put all our eggs in one basket, so we’re always looking at innovative and evolving technologies.
Right now, that includes HVO and we continue to monitor a hydrogen/diesel dual fuel vehicle in service. This was our first venture into hydrogen power back in 2017, with the support from hydrogen technology specialist – ULEMCo. When we launched our first ultra-low emission hydrogen diesel dual-fuel waste collection vehicle, it was another first for the commercial waste industry, and we’ve continued to pursue the hydrogen option ever since.
However, this does come with the problematic issue of obtaining the fuel (hydrogen), as fuelling options are limited around the country. The infrastructure needs to be improved for this to gain further traction
However, one solution we are actively looking at, is if it will be possible to power hydrogen-fuelled vehicles from hydrogen produced by waste treatment processes, which would be another great example of the circular economy in action.
Q: Grundon is at the forefront of transforming waste material into power. Could you explain more about your Lakeside EFW facility and how it has helped with implementing electric vehicles within your fleet and with powering the wider community?
We are fortunate that, as a waste business, we own and operate many of our waste treatment facilities.
The non-recyclable waste that our vehicles collect goes into our Lakeside EfW plant, a joint venture between ourselves and Viridor, one of the largest resource management companies in the UK and part of the FTSE 250 Pennon Group plc.
The EfW process is recognised as a much more sustainable solution for managing waste – it provides 100% diversion from landfill – all the while generating electricity.
The facility currently processes around 450,000 tonnes a year of waste, collected from local authorities and businesses across the region. It goes into a combustion chamber where it is incinerated at 1,000 degrees Centigrade and the heat that is generated powers a steam turbine that generates 37MW of electricity to the National Grid, enough to power around 56,000 homes – equivalent to a town the size of Slough.
Each of the electric waste vehicles collects an average of five tonnes of waste per round and for every tonne of non-recyclable waste deposited, the EfW generates around 620kW of power. Over the course of a day, it means the EfW is capable of generating 3,100kW of energy per vehicle.
Setting aside 280kW to recharge each vehicle, this still leaves a further 2,820kW of electricity for export to the National Grid on a daily basis – enough to power an average-sized house for a year.
We now have the first of our all-electric repowered refuse collection vehicles operating from our base at Colnbrook near Slough, serving commercial customers across London and the wider Thames Valley.
What makes this one different to any others – and we believe is a first in the UK – is that because the Lakeside EfW facility is adjacent to our Colnbrook-based depot, we have been able to install an EV charging point directly at the side of the EfW.
The Colnbrook EV comes back after its early morning or evening rounds, deposits its waste and plugs straight in – literally the circular economy in action. Eventually we plan to run a direct feed from the EfW to the depot so the entire Colnbrook operation will become energy self-sufficient.
A second electric waste vehicle at our Bristol depot is serving customers across the city, and a third is shortly due to start collections in Reading and Newbury from our base at Beenham, in Berkshire. Three more repowered electric vehicles will come into play later this year and go into service in Oxford, a second one into London and the third into the Banbury area.
Our other EVs are all powered in the traditional way, using electricity drawn from the National Grid and, as we add more EVs, so the number of charging stations will increase.
Q: We understand you have recently undertaken the conversion of some of your RCVs to electric. This is obviously a great recycle and reuse project and sits well within your company’s ethos, but how complicated was the procurement process and how did you utilise the expertise of industry partners or suppliers to achieve this?
It’s fair to say that it’s been quite a lengthy process, due in no small part to the availability of the batteries themselves caused by component shortages off the back of the pandemic.
The decision to start integrating electric vehicles into our waste collection fleet was taken as far back as 2021 but we also knew we had to do our homework and get it right first time. We couldn’t afford to let our customers down because we had rushed into the technology.
We already had a long-standing relationship with RVS, which in turn, introduced us to the all-electric repowered refuse collection vehicle they had developed as a joint initiative with Dutch company EMOSS, specialists in converting diesel vehicles into electric vehicles.
Together with a team from RVS, we went over to visit the EMOSS factory and see their work for ourselves, spending time with their technical experts looking at the performance of different vehicles and determining the best technology to suit our needs.
We owe a debt of gratitude to both the RVS and EMOSS teams for their expertise and experience which has helped us at every step of the way.
Q: As a business, how far along are you on your journey to achieving Carbon neutrality and are there any current barriers that you feel could hinder the business in its achievement in the short to medium term?
If I were to say that there were any barriers, it would be around the vehicles we have within our fleet that could and can be repowered. With the incoming legislation operating in London around the direct vision standard (DVS), we are heavily restricted in what we can repower.
We have a number of vehicles that can be converted, and these are currently going through the programme to electrification. The weight of the vehicles, or more specifically the weight of the additional batteries is a concern, however this may change in the near future allowing up to 2 tonne offsetting the weight of the batteries enabling payload to be achieved.
We know our customers make decisions based on a provider’s commitment to environmental issues – so everything we do is about meeting that goal and demonstrating our own progress on the carbon agenda.
We have been measuring our own company-wide carbon footprint since 2000 and since then we’ve reduced carbon emissions by almost 80% through a series of measures, including an ongoing energy self-sufficiency program and investment in state-of-the-art technology.
This is at the same time as growing the business by over 270% and more than doubling our number of employees.
In many ways, achieving that final 20% reduction to reach net zero is likely to be the hardest target of all, but it is one we continue to work towards, both for ourselves and for the benefit of our customers.
Obviously, the work to divert our vehicle fleet away from fossil fuels is a key part of our journey towards net zero and I come back to the comment I made about only being able to move as fast as the technology is available. We keep a very close eye on sustainability developments and are very much about continuing to increase efficiency throughout the business.
For more information visit: www.grundon.com
This fleet in focus was featured in the Issue 5 of Essential Fleet Manager – read it here
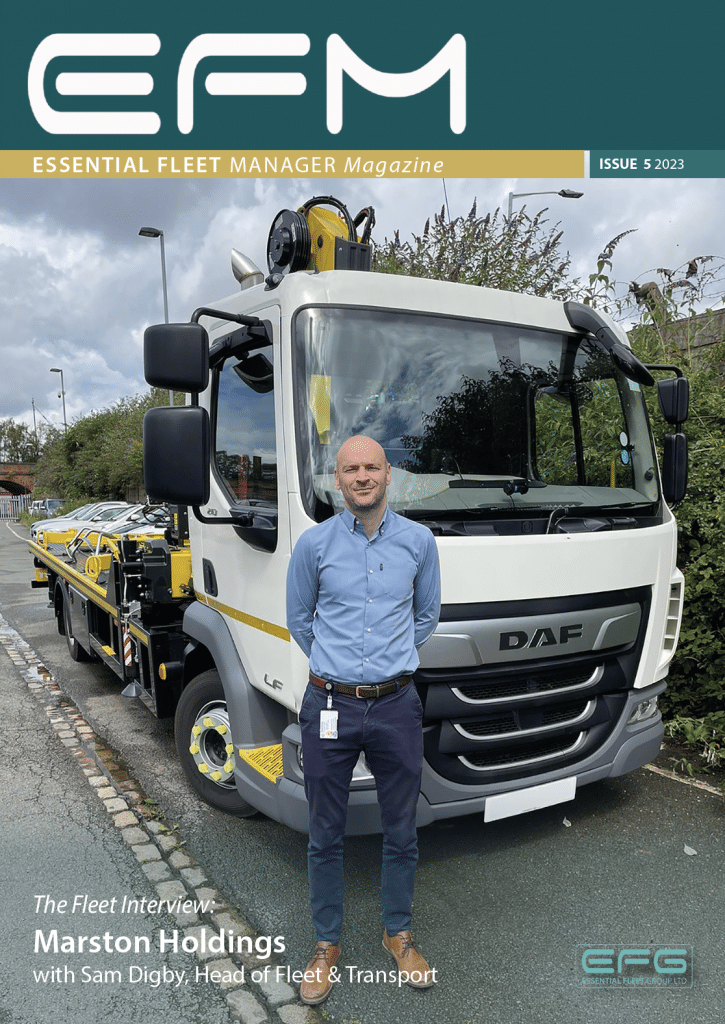